Understanding Slag Removal: How To Improve Metal Quality And Safety
31 March 2025
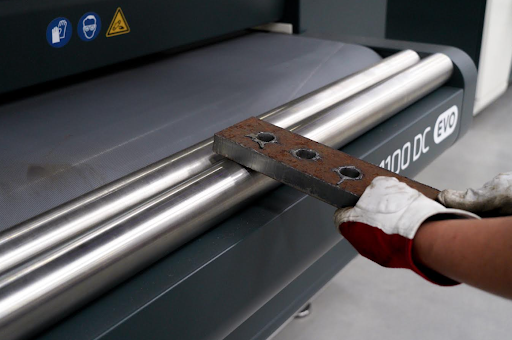
If your business deals with any kind of smelting operation, cutting or working with steel in any capacity, then you almost certainly know all about slag. Removing this unwanted waste material can be challenging and potentially hazardous, but it is an essential part of the metal manufacturing process.
Slag forms when impurities within the steel separate from the molten metal. It typically consists of various types of silica and limestone, although other materials are frequently present, such as sulphur, phosphorus, and various metal oxides. If slag is not removed before the metal cools, it can solidify on the surface, creating rough edges and inclusions that compromise the material's integrity. These defects then require additional processing such as deburring, adding cost and time to the manufacturing process.
The removal process can take many forms, but not all methods are equally efficient or effective. While manual removal using hand tools is possible, it is time-consuming and labour-intensive. Fortunately, various automated solutions can help remove slag safely and effectively, improving both productivity and final product quality.
Below are some of the key reasons why effective slag removal is so important:
Enhanced Purity & Strength
Removing slag eliminates impurities in the metal, ensuring a higher-quality, more durable final product with a smoother surface finish. Slag inclusions can create stress points within the metal structure, potentially leading to premature failure under load. With effective slag removal, your metal products will be stronger and more resilient, maintaining their structural integrity throughout their service life, regardless of their application in your manufacturing processes.
Prevent Welding & Structural Defects
Residual slag that remains after welding or cutting processes can cause weak welds, cracks, lack of fusion, porosity and other structural failures. These defects can significantly reduce joint strength—sometimes by up to 50% compared to properly cleaned welds. Thorough welding slag removal is therefore essential in construction, shipbuilding, aerospace, automotive manufacturing and other industries that rely on the quality and reliability of metal components.
Improved Workplace Safety
Slag that is not removed properly can create sharp or rough edges which pose significant risks to both operatives and end users. Effective slag removal reduces sharp debris in the workspace and minimises injury risk. Moreover, certain types of slag, particularly those containing heavy metals or reactive compounds, can release harmful dust or fumes when disturbed. Proper removal prevents these hazardous chemical reactions, creating a safer working environment.
So, now we have established why slag needs to be removed, what are the most efficient and effective methods for doing so?
Types Of Removal Methods
There are various methods for removing slag, and the most suitable will depend on the specific metallurgical process, material type, and the ultimate requirements of your project:
Mechanical Methods:
-
Grinding: Using abrasive wheels to physically remove slag layers
-
Chipping: Employing pneumatic or manual hammers to break away solidified slag
-
Wire brushing: Effective for removing thin layers of slag and surface oxidation
Thermal Methods:
-
Oxygen lancing: Directing high-pressure oxygen to burn away slag deposits
-
Plasma cleaning: Using high-temperature plasma to vaporise slag contaminants
-
Laser cleaning: Precise removal of slag through laser ablation without damaging the base metal
Chemical Treatments:
-
Acid pickling: Immersing parts in acid solutions to dissolve slag and oxides
-
Fluxing agents: Adding compounds that bind with impurities to facilitate removal
Automated Solutions:
-
Shot blasting: Propelling abrasive media at high velocity to clean metal surfaces
-
Robotic slag removal: Programmable systems that can clean complex geometries consistently
-
Ultrasonic cleaning: Using sound waves to remove fine slag particles from intricate parts
Choosing the right removal method is key to efficient slag management. Additionally, optimising initial welding parameters, implementing regular inspections, and providing comprehensive staff training can all help reduce slag build-up in the first place. This proactive approach improves process efficiency and reduces waste, which is excellent news for both operational effectiveness and your business's bottom line.
Whether you want to understand how to remove slag from your parts or upgrade your metalworking processes with advanced equipment, Sparx Machine Tools can help. Contact our team today to find out more!